|
Comment réalise-t-on l’impression 3D ou fabrication additive ?
Rubrique(s) : Question du mois
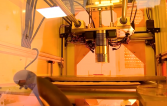
L’impression 3D encore appelée couramment Fabrication Additive (FA) a quitté le domaine du prototypage dans les années 1980 pour gagner le domaine industriel et même le domaine ludique après les années 2000. Elle consiste à réaliser des pièces en 3 dimensions par ajouts successifs de couches de matières principalement des polymères ou des métaux. Elle s’oppose donc à la fabrication soustractive dont le principe est de retirer de la matière à une pièce préalablement moulée (1).
Elle présente de multiples avantages : elle repousse les limites de la technologie en réalisant des formes complexes jusqu’ici irréalisables par moulage ou forgeage, elle permet d’optimiser la quantité de matière première et donc de réduire les coûts et elle permet aussi de réduire les déchets.
Quels sont les procédés de Fabrications Additives ?
Le principe repose sur celui des imprimantes à jet d’encre que l’on retrouve dans tous les bureaux, sauf qu’ici on ne projette plus d’encre chargée en noir de carbone mais un polymère fondu ou une poudre métallique. De même, la buse de projection ne se promène plus de droite à gauche au-dessus du papier (2D), mais elle est animée d’un mouvement vertical au-dessus d’un plateau qui bouge horizontalement (3D).
- FDM (Fused Deposition Modelling) est le procédé le plus connu. L’imprimante est alimentée par un filament de moins d’un millimètre de diamètre d’un thermoplastique qui passe dans une buse chauffée à environ 150° à 250°C. Commandés par un logiciel qui contient les données géométriques de l’objet à fabriquer, les mouvements du plateau et de la buse construisent l’objet couche après couche. Des bobines de fils de PLA (acide polylactique) biodégradable, d’ABS (acrylonitrile butadiène styrène) ou de PET (polyéthylène téréphtalate basse et haute densité) sont maintenant disponibles très couramment chez les industriels des polymères et en 2009 l’expiration des brevets FDM popularise cette technique et lui donne un fort développement.
- Autres types de procédés dérivés du FDM :
- FTI (Film Transfer Imaging) utilise un photopolymère ; après dépôt on illumine avec des lampes infrarouges ou un laser UV pour durcir les couches de résine (SLA StéreoLithography Apparatus) ;
- MJM (Modelage à Jets Multiples) dispose de plusieurs buses et des arrivées de mélanges pour avoir des couches de polypropylène et d’acrylates ;
- SLS (Selective Laser Sintering) quitte le domaine des polymères pour la métallurgie. Des couches successives de poudres de métal (aluminium, acier, titane…) sont déposées et sont frittées par un laser IR de puissance (2). Avec les brevets sur le SLS qui ont expiré en 2014, nombre d’entreprises se sont lancées avec des ateliers entiers d’imprimantes à la fabrication de pièces complexes en petites séries pour l’automobile, l’aéronautique et le spatial.
- Autres types dérivés du SLS :
- le SLM (Selective Laser Melting) : on fait fondre à haute température le fil métallique et on dépose des couches de métal fondu.
- le WAAM (Wire Arc Additive Manufacturing) est un peu une déviation de la soudure à l’arc, puisque le fil est une électrode mise en fusion par arc électrique et le métal fondu est déposé couche après couche. Ce procédé s’est fortement développé depuis 2020.
- le MBJ (Metal Binder Jetting), une nouvelle variante, consiste à projeter des gouttes de liants sur un lit de poudre métallique pour l’agglomérer, puis à passer la pièce dans un four de frittage ; le liant est alors brûlé et la pièce consolidée. L’avantage est que l’impression se fait à température ordinaire, et que l’on peut en faire des centaines en même temps : c’est la voie conduisant aux grandes séries.
Les applications
Les applications sont nombreuses.
Beaucoup de petites pièces d’électroménager sont fabriquées en plastique (polyéthylène, rilsan, nylon). Une fois le logiciel d’impression configuré, les imprimantes alimentées par des bobines de résines fonctionnent toutes seules ; la main d’œuvre est réduite ainsi que les coûts de fabrication. Dans les années 2000, la baisse des prix sur les imprimantes grand public de 200 € à 600 € et la possibilité de mutualiser des scanners 3D et des logiciels d’impression gratuits ont multiplié les « fab lab » dans les établissements d’enseignement ou les maisons de la culture. Après quelques années d’emballement, la FA s’est plutôt développée dans l’industrie et le « hobby » est devenu un épiphénomène.
En métallurgie et en matériaux composites, de nombreuses industries l’utilisent soit en sous-traitant à des ateliers spécialisés en FA, soit en interne pour des pièces complexes comme les hélices creuses pour les bâtiments de Naval Group fabriquées par WAAM ; ceci permet de réduire les stocks et les délais d’approvisionnement. Autre exemple : Constellium, le leader français sur l’aluminium commercialise une poudre d’aluminium Aheadd® CP1 étudiée spécialement pour les pièces des bolides de F1.
Dans le sport (3), pour la chaussure tout terrain de rugby et de football « Shark ONE », la semelle, les renforts et la forme ont été imprimés en 3D en PA11 (polyamide 11 ou rilsan) et Pebax® (constitué de blocs de polyamide et de polyéther), des matières éco-responsables de la société Arkema.
En défense, l’armée américaine a développé des mini-usines qui se déplacent sur le terrain avec des imprimantes 3D pour la fabrication de pièces cassées ou manquantes dans l’armement des armées sur le front. En Ukraine, des drones civils ont été modifiés pour porter des charges et de l’armement.
On se rappelle qu’au milieu des années 2000 un logiciel et les données 3D ont été mis sur le Net par un étudiant américain permettant de fabriquer un révolver presque en totalité en plastique et tirant de vraies balles. En 2025, les spécialistes de la lutte anti-terroriste nous mettent en garde sur la facilité et la disponibilité de telles fabrications sur la toile ou sur les réseaux sociaux à des fins criminelles.
Dans le domaine médical, l’extrapolation du prototypage rapide utilisé depuis plus de 30 ans a été un réel progrès pour l’odontologie et la chirurgie. À l’aide des images de l’IRM, on peut fabriquer des prothèses sur mesure et précises, même complexes (mâchoires, articulations de hanches, genoux…) assez rapidement et parfois en temps réel.
On est près de la science-fiction quand on parle d’impression d’organes humains.
Une société lyonnaise s’appuyant sur des découvertes du CNRS imprime de la peau (4). On prépare d’abord la bio-encre avec des cellules de peau, de la gélatine, un peu d’alginate et de fibrinogène. On passe ensuite à l’impression sur un support en atmosphère stérile puis dans un incubateur durant 21 jours. On imprime ensuite le derme par-dessus avec la même encre. Cette peau imprimée peut servir aux essais des firmes biopharmaceutiques pour les crèmes et cosmétiques, évitant les tests sur animaux.
La construction n’est pas en reste. La fabrication additive permet de construire des bâtiments. Un très beau projet réalisé en 2024 sur les composites résine–bois regroupant deux industriels de la charpente et de la FA, en collaboration avec l’École du Bois d’Épinal et l’École d’Architecture de Nancy ,vise à réaliser la première machine de « stratoconception » de 20 à 30 mètres pour des halls ou salles de sports.
Quels défis pour la FA ?
L’impression plastique continue à se développer mais elle doit tenir compte du recyclage des fils polymères dans une démarche d’économie circulaire menée par les chimistes. Les procédés de la FA sont ceux qui ont le moins d’impacts sur l’environnement, moins de matière, pas de déchets. Mais lors de la conception des logiciels d’impression, les algorithmes de l’intelligence artificielle peuvent optimiser les structures des pièces à fabriquer, en vue de performances spécifiques. Cette nouvelle application de l’IA commence à diffuser.
Le dernier défi à relever concerne la formation et le recrutement car on demande de plus en plus de compétences (5) dans ce domaine où chimie, polymères et matériaux sont les mots-clés pour cette industrie 4.0. Des salons sont consacrés à l’impression 3D où des acteurs du secteur présentent leurs réalisations et recrutent, comme le salon 3D Print à Lyon, par exemple.
Jean-Claude Bernier et l’équipe Question du mois
Pour en savoir plus
(1) La 3D, troisième révolution industrielle ?, J.-Cl. Bernier L'Actualité Chimique (juillet 2015)
(2) Le Laser en contexte industriel : une palette d’applications étonnantes, T. Engel, Colloque Chimie et lumière, Fondation de la Maison de la Chimie (février 2020)
(3) Le rôle des matériaux composites dans les performances sportives, Y. Rémond, Colloque Chimie et Sports en cette Année Olympique et Paralympique, Fondation de la Maison de la Chimie (février 2024)
(4) L’impression fait peau neuve, J. Leyes et B.Robert, Grand Prix Jeunes Journalistes de la Chimie 2018 (vidéo et article)
(5) Voir l’Espace Métiers de Mediachimie
Crédit illustration : capture vidéo L’impression fait peau neuve, J. Leyes et B.Robert, Grand Prix Jeunes Journalistes de la Chimie 2018